The Black Swiss Mechanical Watches for Men Wryst Racer SX1
The Mechanical Black DLC Coated Wryst Racer SX1
This mechanical watch screams luxury, boldness, and dedication to racing sports. The SX1 with black Diamond-Like Carbon casing is the only luxury Swiss automatic wristwear with DLC protection at this price tag. Initially fitted with the black and grey leather bracelet, you can also enjoy wearing your stunning Racer with a black silicone quality band and the Swiss movement sellita sw200. Two bracelets are systematically included when you buy a Wryst.
Only 75 people will ever wear one of this small limited edition series of dress watches. Black is the color used to convey authority and certainty. Feel assertive and ready to get behind the wheel with a Swiss black automatic timepiece that won't leave anyone indifferent.
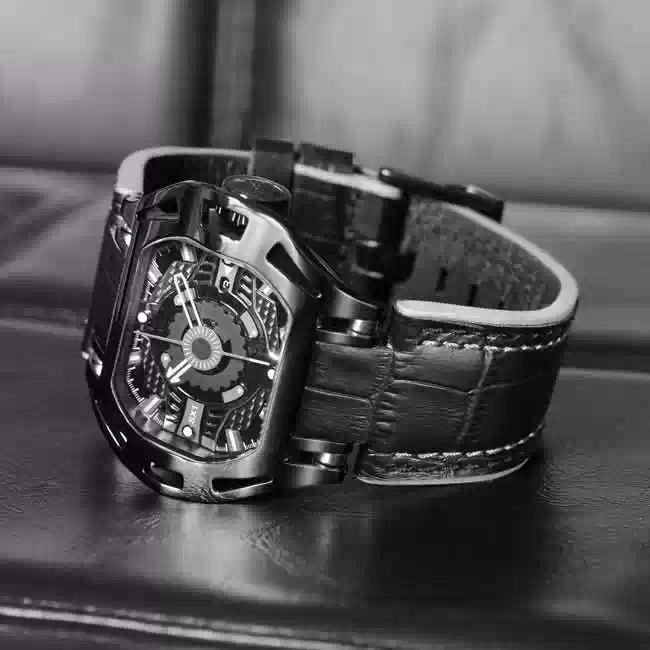
Renowned Swiss Mechanical Movements
The Sellita SW200 movement is the twin brother of the workhorse ETA 2824-2. The Sellita watch movement offers winding watches with a competitive power reserve. The rotor's gear train winds the mainspring, so the balance wheel distributes the required impulse to the hands.
The watch case
The mechanical watch body features ergonomic edges on the bezel. An intricately curved casing holds the exciting three-dimensional dial. The right side covers and protects the winder entirely. One can admire the sellita SW200 movement on the back through a smoked crystal printed with the manifold-style Wryst logo. Two case lugs in the shape of a camshaft provide a solid attachment to the bracelet with a secure height-set screw system. This patented watch feature guarantees that your watch will not detach from your wrist accidentally.
The Two Different Bracelets
You will enjoy the Wryst mechanical watch Racer SX1 in two different versions.
The first is a luxury hand-made black leather bracelet with three different layers. The band is finished with leather and double stitching, with a line in black and another in grey. The inner side is within a soft suede-style finish for maximum comfort—a stamp press debosses the mention of "Genuine Leather" with the brand's logo. On the side, the third leather decorates the bracelet edges with cowhide grey leather.
Secondly, thanks to the other band also available with your purchase, you can choose a modern double injection silicone band, highly flexible silicone. This large band is 25 mm, and with a soft backside, the comfort has been optimized for a seamless experience on your arm. If most of our two-tone bracelets offer a contrast of two colors, we opted for both colors in black for this reference.
Mechanical watches are all about wheels, gears, springs, jewel bearings, and oils working together with only the physical laws of mechanics to govern the interactions between all the components. This rare complexity mastered by the human brain and hands creates all the appeal, mystery, and prestige of mechanically engineered watches.
A Fascinating Piece of Engineering
All mechanical watches continue to fascinate for many reasons, starting with the tiny size of their elements. Indeed, the measuring scale here is a micron or one-thousandth of a millimeter (0.001 mm). To understand what that means better, consider that one of your hair measures between 0.06 to 0.07 millimeters.
Until the nineteenth century and the improvement of machining tools, building a watch was a craft in which only specialists could design the movement, manufacture the components, assemble them, and make it all work. Such individuals still live among us today, even if they are scarce. Each of their tasks has become an appropriate field with an outstanding specialization.
The complexity of movements has also increased significantly, making it sometimes impossible to apply the traditional ways of conceiving and creating watches using pencils, paper, and drawings.
A Close Look at the Mechanical Watch Movements
Calibers are created by movement designers and engineers using computers similar to those found in automotive engineering. Micromechanics is in charge of programming the computer numerical control (CNC) machining tools, which carry out parts production. Then watchmakers finish, assemble, test, and adjust the movements before fitting them into cases, adding the dial and hands, and closing them up.
Many tests are necessary to check the quality at different stages because of the complex manufacturing process and level of detail required. Dedicated craftspeople can also execute the various tasks separately. For instance, the assembly of a movement can fall into subgroups of parts with specialists in charge of assembling them. The experienced watchmaker focuses only on the most sensitive operations.
Art and decorative craftsmanship also find their way into movements. Mirror polishing, beveling, engraving, and even gem-setting are the usual techniques applied in fine watchmaking to embellish the mechanics by creating visual contrasts between the various parts and their surfaces.
Evolution and Improvements
Even if it is true that the principles of their design haven't significantly changed since the nineteenth century, watchmakers and engineers always work on improving the reliability and precision of movements.
Watchmakers from Switzerland have perpetually integrated innovations at every level in this quest, whether with materials or engineering processes. Experimental techniques have emerged that, for instance, allow moving parts to be almost floating, thanks to micro magnets creating a small magnetic field.
This helps reduce friction between classic metal parts. Some parts are built-in carbon fiber or ceramics-for instance, with ball bearings. Other components are coated with a layer of artificially grown diamond for protection. Silicon has made more and more inroads in fabricating crucially sensitive and thin elements like the hairspring, the pallet lever, and the escape wheel. Very rarely do these new materials allow for new mechanical watches for men.
Structure of a mechanical movement
A mechanical movement can be imagined like a sandwich with lower and upper parts dedicated to securing all the moving parts (like wheels) between them.
Base plate
The base plate is the stable base of the movement. It usually looks like a flat coin with plenty of cavities and holes to allow space for moving components and screws.
Moving elements
The moving parts are mainly located in the heart of the movement. Some can be placed outside the base plate to highlight them.
Bridges
Bridges are sandwiched on top of the moving parts. They can also have holes for screws to go through that secure them to the base plate. The shapes of bridges and their configurations are like pictures on ID cards. Each says a lot about the movement, and connoisseurs can recognize specific movements and watches by looking only at their designs and particular elements. You may be able to do that one day!
Functioning
A mechanical movement is a system composed of interconnected cogwheels. The forms of their teeth, as well as their diameters and sizes, generally differ based on their roles. That is why a caliber can look so complex and confusing. To fit into a case, this set of components assembled much like a puzzle is conceived to occupy a minimum spatial volume.
Without this constraint, a mechanical movement could be constructed in a line, for instance, with each element ends to end next to each other. At one end, you would find the drum barrel (alias the energy store); in the middle, a series of a minimum of three cogwheels forming the gear train (for energy transmission); and at the other end, the escapement and balance for portioning the energy into segments.
Power
As a child, did you ever play with toy cars that had to be wound using a key to run around the floor until their energy was used up, or have you at least seen these in a television ad? A mechanical watch works the same way, except the power lasts much longer because of the regulator subassembly. (A toy car does not have this regulator, which is why the power runs out so quickly).
In a mechanical watch, energy is stored in the mainspring, which is located inside the spring barrel, a small round container that revolves around an axis called the barrel arbor; it drives the gear train.
Made out of a special metal alloy, the mainspring is created with a particular manufacturing process. At one end, the spring is fixed to the center of the barrel arbor. Its mission is to unwind, releasing tension and thus energy as regularly as possible, no matter the conditions and stress level.
The barrel arbor is the part that rolls the spring up around itself, thereby creating tension. It is activated by the barrel's ratchet wheel, a cogwheel placed outside the barrel, and directly linked with the manual or automatic winding system.
At the other end, the mainspring is fixed on the side of the barrel drum that powers the gear train thanks to external toothing. The mainspring can end with a slipping spring gliding along the barrel to avoid breaking from excess winding. That system is often found in older watches; the mainspring is usually secured to the barrel in newer timepieces.
Power reserve
In a mechanical movement, the available power reserve (the number of hours the watch is supplied with energy) depends on various factors. The length of the mainspring has a significant impact. And in certain watches, the mainspring can measure more than one meter!
Watchmakers can also add several spring barrels, comparable to putting several gas tanks in a car. Recent high-end mechanisms can house up to eleven barrels for a total power reserve of fifty days - more than a month and a half! A regular mechanical watch caliber usually has a power reserve of about 42 hours. The winding system has a direct influence on the conception of the caliber.
Remember that a longer power reserve on a manual winding watch is a positive thing: If the owner must wind a watch less frequently, it saves the mechanism from excessive wear and tear. The benchmark set for some years now is eight days of power reserve. Why such a length? First, it makes sense because some enthusiasts own more than one watch and generally change them on the weekend. As they don't want to set a watch each time they pick it up, they like to have a power reserve that lasts for at least one week.
Last but not least: Keep in mind that the duration of the power reserve provided by the brand usually corresponds to the period during which the torque is strong enough to ensure the watch's precision, but it will most likely run longer.
Manual winding
The manual winding system was the first one invented, and it is the simplest version: Energy enters the movement from an external source. Owners needed a key or another tool to wind the movement in old watches. That is still the case with many wall clocks, for instance. In 1820, an English watchmaker named John Arnold invented a little external element that allowed the wearer to wind the barrel: the crown. The gold standard today, the crown is generally positioned on the same side of the watch as the vital spring barrel elements. Note that you can wind every mechanical movement-even automatic, examples-using the crown.
Automatic winding
Automatic movements are as clever as they are practical. It's true; turning your crown regularly to wind the mainspring can be tedious and take up your time, and it goes without saying that if you forget to do it, your watch will stop working without you noticing it. Comfort and a need for particular security regarding energy reserves inside the caliber motivated watchmakers to invent self-winding systems. The first watches, including a self-winding system, were created at the end of the eighteenth century. But today, mechanical watches for men outnumber manually wound ones, with good reason.
From the beginning, the idea was to use the motion of the owner's body, and in particular their wrist, to generate energy. To do so, watchmakers added a mobile element to the back of the movement that oscillates back and forth. This part, called the rotor or the oscillating mass, has the approximate shape of half a disk and revolves around an axis. The rotor is directly connected to the spring barrel via a gear. Some systems wind only in one direction of oscillation, others in both; this is a movement designer's choice.
On specific movements, the rotor makes some noise when moved, which can be considered a kind of signature element. And if you pay close attention, you can usually also physically feel the motion of the rotor when you wear the watch. The result is the same, except it takes a little bit more time to wind a movement fully with a unidirectional system.
Note that most of the time, the axis for the rotor is situated in the center of the movement-but, not always. Some models, and only some, are equipped with micro rotors. Micro rotors are smaller examples that make their revolutions not above the movement but within it. These are chiefly created to reduce the height of a movement and are much more challenging to manufacture and adjust.
The Regulation:
Escapement and oscillator
The mechanism's goal, usually called "the escapement," is to regulate the flow of energy from the barrel through the gear train and to split it into regular impulses to count time. You can see this action played out on the dial. Indeed, if you have a long second hand on your watch, note that each almost imperceptible step it takes forward is the result of one impulse. The regulating system is a set of parts that are very accurately made and adjusted; its precision is passed on to the act of time measurement.
Strictly speaking, the regulator is divided into two major subassemblies: the oscillator and the escapement. The oscillator acts in combination with a large, light wheel called the balance wheel and an ultrafine hairspring rolled into coils and located in the middle.
These two components are the most delicate and sensitive in any mechanical watch. Their manufacturer is the most powerful personal brand they hold on to, and professionals who work on them are rare, gifted, and very much in demand in the industry. One end of the hairspring is secured to the balance staff, while its other extremity is connected to an external and immovable attachment point. Its role then oscillates, turning in one direction before coming back to create impulses.
The escapement subassembly comprises the escape wheel, pallet lever, and pallets. It portions the energy and sends it to the oscillator. Working together, the oscillator and the escapement transform the linear flux of energy into pulsations that give rhythm to the entire movement. The speed of these oscillations provides the frequency of the caliber. And the higher it is, the more precise it becomes.
Jewels and shock absorbers
A mechanical movement's various wheels and components must turn as quickly as possible; any friction represents a loss of energy and precision.
For this reason, watchmakers use synthetic rubies called jewel bearings to maintain the ends of the axes with as little friction as possible. These jewels are minuscule carved disks with or without a tiny hole in the middle.
Historically, a Swiss mechanical watch was made out of natural ruby; now, they are the purer synthetic ruby. Thanks to their artificial manufacture, colors can also vary from the original red. Usually, the number of jewels a movement contains is engraved on the movement.
The rubies maintaining the most sensitive axes-like the balance wheel, for instance-are, are usually doubled with a shock absorption system. This component mainly has the shape of a circular microblade spring positioned within a fixed part where the jewel is located.
All references "RACER" with two silicone bands:
Self Winding Watch SX1
Luxury Gold Watches for Men SX2
Automatic Gold Plated Watch SX3
Automatic Racer Watch SX4
OTHER AUTOMATIC REFERENCES HERE
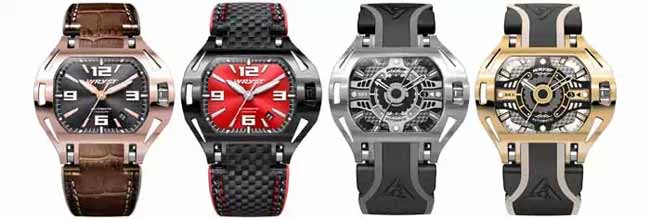